|
References I Project portfolio |
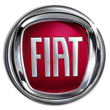
|
FIAT - 2012 in partnership with KRAGUJEVAC - Serbie
The Italian car manufacturer decided to renovate the old ZASTAVA factory, situated some 100 kilometres south of Belgrade, to manufacture the new FIAT 500 and 500L. EISENMANN won the contract for the entire renovation of the paint workshop and chose PaintSys as its partner for the turnkey completion of the dust-removal machines consisting of a blower gantry at the input to the primer line and a BLOW OFF / EMU unit at the input to the lacquer line.
|
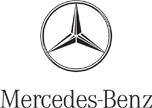
|
DAIMLER - 2012 in partnership with JUIZ DE FORA - Brésil
As part of the production redistribution of its various models, Mercedes-Benz modified the manufacturing lines in its factory at Juiz de Fora (400 km to the north of Sao Paolo), which originally made C-Class vehicles, so as to be able to manufacture trucks. PaintSys supplied two gantries for blowing ionised air that were set up at the start of the primer and lacquer lines.
|
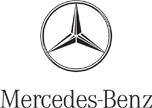
|
DAIMLER - 2012 in partnership with PEKIN - Chine
Having decided to increase its production capacities in China, Mercedes-Benz invested in a new factory in Beijing. ABB won the contract to supply paint equipment and selected PaintSys for the turnkey installation of the dust-removal machines. With the help of its network of Chinese partners, PaintSys delivered and commissioned three complete BLOW OFF / EMU units for the primer line and the two top coat lines.
|
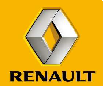
|
RENAULT - 2012 SANDOUVILLE - France
As part of the reorganisation of the RENAULT production lines in France, the Sandouville factory will be called on to manufacture utility vehicles from 2014. As a result, the French manufacturer decided to invest heavily to transform its production lines. PaintSys won the contract to modify the dust-removal machines on the lacquer line and the counter-stamp line. Pre-production is scheduled for 2013 and increased production will begin in the first half of 2014.
|
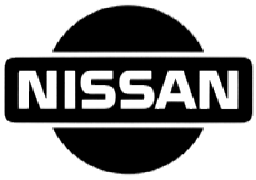
|
NISSAN - 2012 in partnership with TOGLIATTI - Russie
PaintSys, in conjunction with EISENMANN OOO, won the contract to extend the number of colours in the bumper paintshop on the historic site of AvtoVaz PPI in Togliatti. PaintSys will supply ten complete units consisting of new high-runner dispensing machines as well as the circulating systems, and will be responsible for related modifications to the existing ABB robots. Commissioning is scheduled for the end of the first quarter of 2013.
|
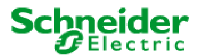
|
SCHNEIDER - 2012 VIEUX THANN - France
As part of the development of the production resources for a new range of medium voltage circuit breakers, PaintSys won the contract for a complete sizing line for SCHNEIDER in Vieux Thann (68). This line, which has been designed in its entirety by PaintSys, will make it possible to size both metal and plastic parts. Entirely automated and autonomous, the process integrates a robotised conveyor system, oven, plasma surface activation and sizing. Commissioning is scheduled for the beginning of 2013.
|
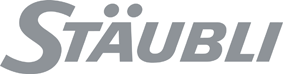
|
STÄUBLI - 2012 FAVERGES - France
STÄUBLI marketed its new specialised robot for painting, the TX250, in 2012. The result of a partnership with PaintSys, the robot has a process arm and a 3-axis hollow wrist; the unit is made from non-conductive materials that makes the TX250 particularly suited to water-based paints. PaintSys delivered a first series of 40 units to STÄUBLI, which integrated them on the proven basis of the RX160 adapted to the inertia of the new forearm.
|
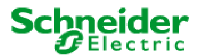
|
SCHNEIDER - 2011 MANISA - Turquie
SCHNEIDER ELECTRIC operates an entire line for metallising parts in epoxy consisting of medium voltage switchgear on the site of MANISA in Turkey. Metallising is carried out by an automatic pistol mounted on a robot in a paint booth. The nickel-based paint was highly sensitive to external conditions, especially temperature (sagging and drying during spraying). PaintSys carried out the air-conditioning of the paint booth and associated mixing room so as to maintain a temperature of below 23°C.
|
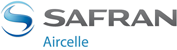
|
AIRCELLE - 2011 in partnership with TOULOUSE - France
The Toulouse site of AIRCELLE assembles engine nacelles for the aeronautics industry. The paint was previously applied manually part-by-part and AIRCELLE wanted to demonstrate the possibility of painting a large, pre-assembled nacelle in its entirety (2 metres in diameter and 3.7 metres wide) using a multi-axis robot. PaintSys developed and commissioned a pilot cell based on a Stäubli TX250 robot for spraying 2K and 3K paint.
|
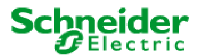
|
RECTIPHASE - 2011 in partnership with PRINGY - France
RECTIPHASE, a subsidiary of the SCHNEIDER ELECTRIC group, develops and manufactures compensation capacitors on the Pringy site in Haute Savoie. The paint was applied to the capacitors entirely by hand but the introduction of a new product range in addition to the former range created an increase in production capacity to justify the automation of the paint process. PaintSys undertook the automation based on a Stäubli TXPaint 90 XL robot by interfacing it with the existing dual-rail conveyor and booth. The completed PaintSys includes a mixing room for the application of 1K water-based paint for the primer and 3K for the finish.
|
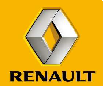
|
RENAULT - 2011 SANDOUVILLE - France
Following the redistribution of the manufacture of its range of vehicles across its French sites, RENAULT re-organised the production lines in the Sandouville factory and commissioned PaintSys with transferring the automatic wiping machine for the lacquer line. PaintSys was referenced as a direct RENAULT supplier.
|
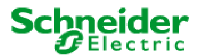
|
SCHNEIDER - 2010 in partnership with MANISA - Turquie
SCHNEIDER ELECTRIC developed a new range of medium voltage circuit breakers whose main components are made of epoxy resin. These parts must be treated to give them surface conductivity. After a first simultaneous engineering phase, SCHNEIDER ELECTRIC and PaintSys defined a range of surface treatments consisting of a sanding phase and a phase for applying nickel-based metallic paint. PaintSys carried out the entire installation corresponding to this range: a dual-rail inverted conveyor, camera-based part recognition system, robotic sand-blasting booth with cyclone recovery, robotic paint booth, mixing room, oven, cooler and VOC treatment.
|
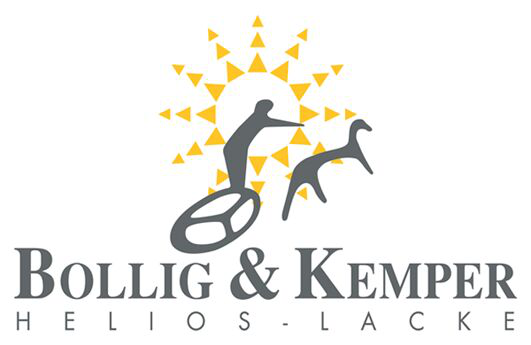
|
BOLLIG&KEMPER - 2010 CHAMP-PRES-FROGES - France
BOLLIG&KEMPER France, supplier of industrial paints, invested in the upgrading of its robotic paint application booth for its R&D laboratory outside Grenoble. This booth must be able to reproduce as best as possible the application conditions encountered on the customer sites, especially in terms of temperature and humidity. PaintSys designed, manufactured and commissioned a new booth with an air treatment unit including filtration, heating and cooling, and humidification.
|
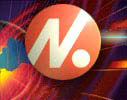
|
INOPLAST - 2010 SAINT DESIRAT - France
INOPLAST Saint Désirat ordered a complete UNIT7 paint line from the Argentinean company GOTTERT mainly for making bumpers. During the implementation of the line, INOPLAST wanted to add low-quantity paint dispensing for small series production. PaintSys was chosen by GOTTERT to study, manufacture, install and commission four rinsable microlines supplied from 25 litre canisters.
|
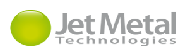
|
JET METAL - 2010 in partnership with SANDOUVILLE - France
JET METAL developed a metal spraying process for all types of supports by means of dynamic chemical deposition. JET METAL wanted to equip its demonstration laboratory with a device for handling volume parts. PaintSys set up a unit for the surface activation of parts to be metallised then the Metal spraying itself and finally the rinsing using a six-axis STÄUBLI 6 RXPaint 90 L robot equipped with four pistols converging on the same point of impact.
|
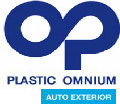
|
PLASTIC OMNIUM - 2009 in partnership with RUITZ- France
The paint line on PLASTIC OMNIUM’s Ruitz site has a booth for cleaning parts manually. PLASTIC OMNIUM awarded PaintSys the contract to robotise the cleaning process using two ABB IRB5402 robots. The robots were equipped with tools for blowing ionised air with a turning nozzle that were specifically designed for this application. They were installed in the booth and integrated into the automation of the line seamlessly for users as well as the fourteen other robots fitting into the process.
|

|
CATERPILLAR - 2009 ECHIROLLES - France
The CATERPILLAR Echirolles site assembles wheeled excavators. CATERPILLAR wanted to make adjustments to the assembly line, in particular concerning the setting up of the driver cabins. PaintSys was selected to manufacture a new conveyor supplying the cabins consisting of triple-channel motorised tables, including one swivelling through 90°. These tables must be capable of supporting a maximum load of 3100 kg.
|

|
METALPES - 2009 SAINT MARCELLIN - France
The METALPES factory at Saint-Marcellin manufactures switch boxes for the electrical industry. It sub-contracts the surface treatment process and therefore decided on an investment programme designed to integrate a complete line including the parts conveyor, preparation tunnel, drying oven, powder booth and baking oven. METALPES wanted to benefit from the support of an experienced company that was independent in relation to equipment manufacturers. It was against this background that METALPES contacted PaintSys as a specialist in surface treatment techniques.
|
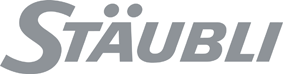
|
STÄUBLI - 2009 FAVERGES - France
STÄUBLI was keen to have a robot with a process arm and hollow wrists to enhance its range of paint robots. STÄUBLI approached PaintSys to synergise its experience in robot design with PaintSys’s experience in the paint industry. The two companies then collaborated on developing the new robot by the name of TX250, which will be put on the market in the coming months. Requirements analysis, preliminary design, 3D dynamic modelling, prototyping and pre-series have been put in place to make the TX250 a well-designed product that makes the difference compared to other paint robots.
|
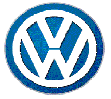
|
VW - 2008 in partnership with SHANGHAI - Chine
VOLKSWAGEN decided to increase its production capacity in China and invested in a new line situated near SHANGHAI. EISENMANN won the contract for the paint workshop and chose PaintSys as its partner for the turnkey completion of the dust-removal machines, which include an entire EMU with pre and post-ionisation units at the input to the primer line and a BLOW OFF & EMU unit at the input to the lacquer line.
|
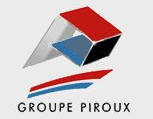
|
GROUPE PIROUX - 2008 in partnership with TREFFORT - France
The PIROUX group paints thermosetting plastic bumpers, fairings and deflectors as a sub-contractor for RENAULT TRUCKS on its Treffort site. These parts equip the Magnum and Premium ranges. The site has a continuous line for white and, in parallel, a manual booth for other colours. PIROUX awarded PaintSys the contract to robotise this booth to improve its productivity and the quality of the parts by controlling the thickness of the paint deposits. The robotisation was carried out by a TXPaints 130 BXL from the Stäubli paint range.
|
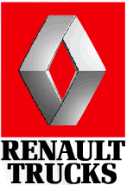
|
RENAULT TR. - 2008 in partnership with BLAINVILLE S/ ORNE - France
RENAULT TRUCKS has incorporated new truck cabs into the commercial range that it manufactures in the factory at Blainville-Sur-Orne. This new range, where the cabs can be up to 3,300 mm, involved the re-organisation of the production lines and, in particular, the surface treatment workshop. EISENMANN secured the contact that consisted mainly of modifying the primer line and manufacturing a new lacquer line. EISENMANN awarded PaintSys the contract to transfer and modify the existing dust-removal station and the turnkey delivery of a new station for the lacquer line.
|
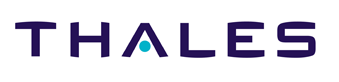
|
THALES - 2008 in partnership with MOIRANS - France
Based in Moiran, THALES ELECTRON DEVICES makes various types of electronic tubes for medical imaging. One of the phases of the manufacturing process consists of manually applying a varnish whose primary function its to ensure the final sealing of the tubes. THALES wanted to automate this varnishing and awarded PaintSys the contract to manufacture a booth equipped with a STÄUBLI TXPaint 90 XL robot. A camera-based vision system identifies the type of tube to be varnished at the start of each cycle. A special conveyor then transfers the tube under the robot in order to carry out the varnishing. The varnish is applied using a pressure tank.
|
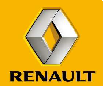
|
RENAULT - 2007 in partnership with SANDOUVILLE - France
RENAULT decided to create a pilot to test the automation of the colourimetric analysis on-line. The pilot was installed in the factory at Sandouville. EISENMANN and PaintSys were selected to make the pilot based on a reconditioned KUKA robot and a CARFLASH colourimetric reading system by XRITE. Colourimetric measurement is performed on 24 pre-defined points on the bodywork.
|
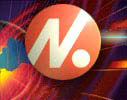
|
INOPLAST - 2007 SAINT DESIRAT - France
INOPLAST UNIT12 wanted to increase the number of colours dispensed over its two base-coat FANUC P200 robots for painting vehicle tailgates. PaintSys carried out the turnkey implementation of eight new colours, including the manufacture and installation of new dispensing machines, their dispensing on the robots’ colour change units and the modifications to the automation systems at the controller robots.
|
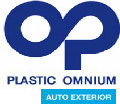
|
PLASTIC OMNIUM - 2007 in partnership with LANGRES - France
PLASTIC OMNIUM wanted to make paint savings on the four basic robots in its factory in Langres. PLASTIC OMNIUM was chosen to use the RETRO CLEAN system made by ITW INDUSTRIAL FINISHING. This system makes it possible to recover the paint during the colour change phases by pushing it back into the circulating system by reversing the rotation direction of the metering pump. It is particularly suitable when the colour change unit is situated at a significant distance from the sprayer. PaintSys was selected to carry out the modifications and to install 4 RETRO CLEAN at Langres.
|